コーマ|繊維の長さをできる限り揃えるため短い繊維を取り除いていく
カードの工程を終え、タイコ状に巻かれた原綿をコーマ機に通す。コーマ機にも針が付いており、下から掻き出すことで短い繊維が下に落ちていく仕組みだ。左下の写真を見れば、取り除かれた繊維とそうでない繊維の長さの違いが明確に分かるだろう。ちなみに、短い綿を残していい意味でのムラ感を生み出すために「コーマ」を通さないケースもある。たとえばデニムに使われるものがそうだ。
ちなみにこの工程で落ちた綿は「コーマ落ち」、ここで機械に残ってスライバーとなった綿は「コーマスライバー」と呼ばれる。コーマスライバーはより糸に近い形状になる。
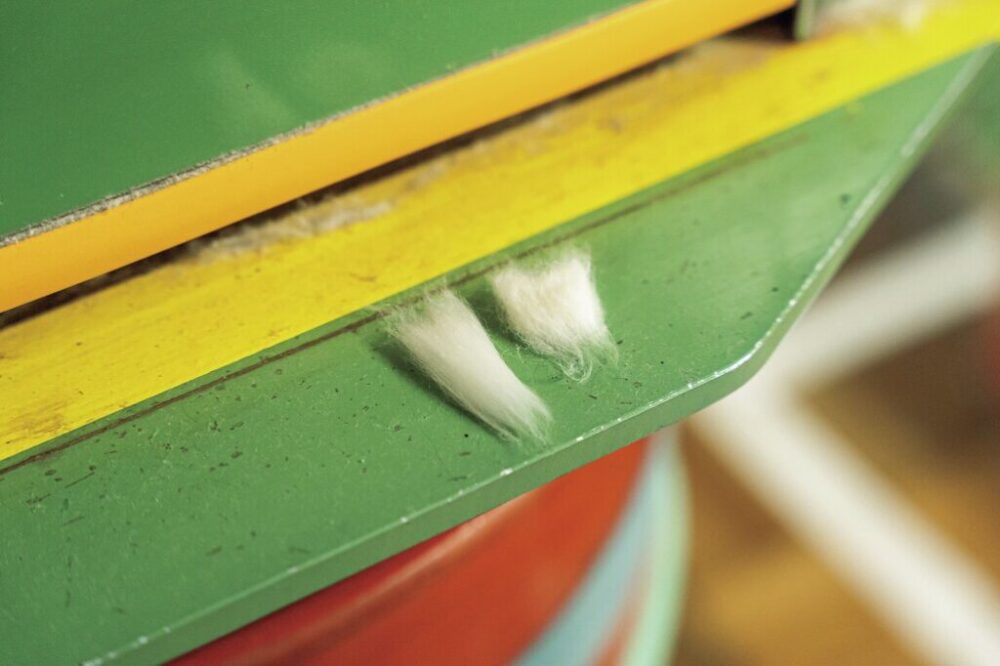
練条(れんじょう)|8本のスライバーを1本にまとめて引っ張ることで、太さを均一にする
カード、もしくはコーマの工程を終えた8本のスライバーを一本にまとめて、「練条機」と呼ばれる機械で引き伸ばす。8本のスライバーを8倍の長さに引き伸ばすことで、練条機から出てくるときは、練条前の1本分の太さになっている。こうすることで太さにムラのあるスライバーが均一な太さに整う。通常この工程を2〜3回繰り返し行う。
強力に圧縮されて出てくる!
粗紡(そぼう)|練条にかけられた束をさらに引っ張ることで、糸に近い状態へ
練条機にかけられたスライバーをさらに8〜9倍の長さに引き伸ばすことで、「完成後の糸」の太さに近づけ、次の「精紡」という工程で糸にしやすくする。この「粗紡」工程を終えた束が、ここで初めて「ロープ状の繊維の集合体」を表すスライバーという呼び名から、「糸」という名称に変わり「粗糸」と呼ばれるようになる。
精紡(せいぼう)|加える力の強さや回転方向で番手と撚りの向きが決まりいよいよ糸が完成する
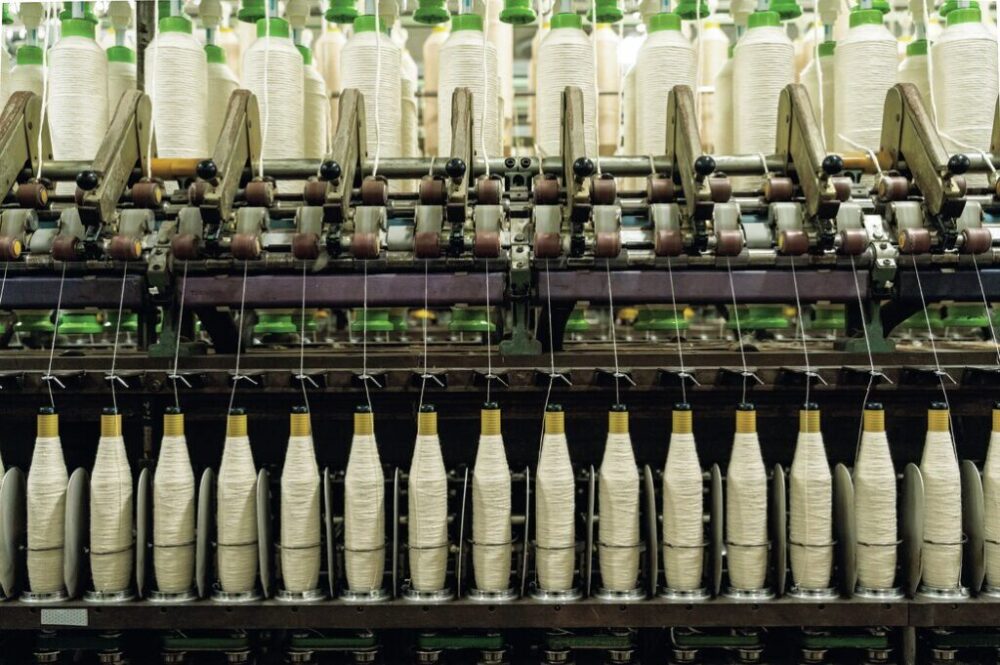
粗糸は30倍ほどの長さにするために引っ張り、ボビンに巻きつけて管糸(かんし)と呼ばれる糸の完成形となる。縦方向に回転するバンドのようなもので糸を押さえつけながら引っ張るのだが、その引っ張る強さで番手を、機械下部に設置された回転するボビンの方向で撚りの向きが決まる。
通称「石川台」と呼ばれる1950年代製の機械は、押さえる力や回転数こそ少ないが、そのおかげで柔らかな風合いやいい意味でムラが生まれる。なお、この機械で紡績されるのは単糸。2本撚りの双糸は別の工場で作られる。
番手は後ろのローラーと前のローラーとの回転の差で確定する。稀に糸が切れることがあるため、職人が見回る。
石川製作所製の「石川台」で、茶綿が精紡されている光景を見ることができるのは、世界でも「大正紡績」だけだ。
(出典/「2nd 2024年5月号 Vol.204」)